Важнейший станок "деревянного" моделиста
Хочу поделиться с коллегами своими мыслями о универсальном
шлифовальном станке, без которого невозможно быстро и качественно выполнять
большой объем работ по созданию моделей из дерева. Хочу отметить, что идея этого
станка вызревала постепенно в процессе постройки моей первой модели.
Первоначально я сам себе выставил следующие техусловия:
-
Станок должен быть универсальным, иметь в качестве рабочего
инструмента и барабан для изготовления реек, и диск для обработки произвольных
деталей.
- Двигатель должен быть достаточно мощный и регулируемый.
- Станок обязательно должен быть оснащен пылеотсосом.
Необходимость регулировать частоту вращения сразу определила
тип двигателя - коллекторный. В загашнике нашелся коллекторный двигатель от
полотёра - 220в, 10000 об\мин, вал в резьбой М8, мощные шарикоподшипники. Была
подобрана готовая втулка с резьбой М8 и фланцем, из 10 мм фанеры склеен диск.
Для фиксации стандартных шлифкругов на диск наклеена текстильная застежка
(<липучка>). И начались эксперименты, в ходе которых выяснилось, что:
- При номинальном напряжении питания двигатель очень шумит и греется.
- При частоте вращения 10000 об\мин дерево не столько шлифуется, сколько горит
и обугливается.
Для решения этих проблем был изготовлен простейший регулятор
мощности на симисторе, что позволило регулировать обороты от 0 до максимума.
Теперь стало возможным подбирать оптимальный режим работы. Вроде, проблема
решена, но приходилось постоянно одной рукой держать деталь, а другой
<газовать>, компенсируя падение оборотов при увеличении нагрузки. Конечно,
постепенно можно приспособиться, но внимание постоянно концентрируется на
двигателе, а не на детали. В общем, вариант был отвергнут.
Следующим шагом стала идея автоматической регулировки частоты
вращения при изменении нагрузки. Идея прекрасная, но как ее реализовать? Все
известные схемы довольно сложные и громоздкие, даже для радиолюбителя с
30-летним стажем, коим себя считаю. И тут где-то на бескрайних просторах И-нета
попалась схема управления двигателем автоматической стиральной машины. Вот где
решение! Ведь в стиральной машине коллекторный двигатель переменного тока и
система автоматического регулирования, и, самое главное, все было реализовано на
одной(!) микросхеме (TDA1085C), специально разработанной для такого применения.
Единственная проблема - у стиральной машины в двигателе есть таходатчик, в
полотёре нет. Пришлось вспомнить старую схему стабилизатора частоты двигателя -
на валу закреплена шестерня, а вплотную к ней магнитная головка от магнитофона.
При вращении шестерня возбуждает в головке ЭДС с частотой, пропорциональной
частоте оборотов и количеству зубьев шестерни. Осталось этот сигнал усилить и
подать на схему от стиральной машины (см Рис.1).
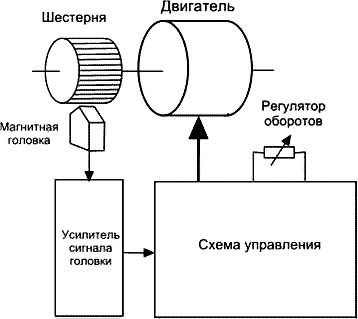
Рис.1 Блок-схема системы стабилизации частоты вращения
Принципиальная схема блока опубликована в статье Блок управления коллекторным двигателем с обратной связью по частоте
После завершения теории переходим к описанию конструкции.
Станок состоит из базового блока-привода и насадок к нему для выполнения
различных операций.
Базовый блок.
Вид со лицевой стороны. Сюда крепятся насадки. Для точной посадки насадок служат
два штифта.
|
Базовый блок.
Вид с обратной стороны. Здесь расположены выключатель, регулятор оборотов и
разъем для подключения пылесоса, позволяющий производить включение пылесоса
синхронно со станком.
|
Базовый блок
со снятой крышкой. Т. к. двигатель часто работает в нештатном режиме (малые
обороты при большой нагрузке), он может перегреваться, поэтому внизу установлен
вентилятор от компьютера, а сам блок имеет вентиляционные отверстия вверху и
внизу. Блок изготовлен из 10 мм фанеры , <моторама> склеена из 2-х
слоев.
|
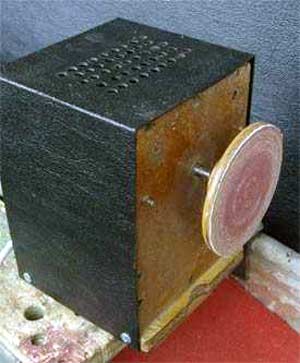 Основные рабочие инструменты, склеены из 10 мм
фанеры. Окончательная обработка производилась прямо на валу двигателя, что
позволило достичь минимума вибрации и биений. Для посадки на вал двигателя
служат стальные втулки с фланцем с резьбой М8, зафиксированные эпоксидным клеем
и шурупами.
|
Насадка №1 для работы с диском. Столик из 3 мм
стали, под диском сформирована полость, которая сообщается с патрубком пылесоса
и служит для эффективного удаления пыли во время работы. Вертикальная щель в
основании насадки позволяет снимать ее, не снимая диска.
|
Для
работы с мелкими деталями служит съемный дополнительный столик.
|
С
помощью дополнительной направляющей можно под определенным углом обрабатывать
торцы реек.
|
Так можно
калибровать не очень тонкие (более 5 мм) рейки. |
Пример работы.
Деталь выпиливается с некоторым запасом, а потом ее размеры точно подгоняются на
станке.
|
Насадка №2 для
работы с барабаном. Предназначена для изготовления реек и шпона. Столик из 3мм
стали правым концом закреплен на петле , левый опирается на винт, позволяющий
регулировать толщину выходного материала 0-30 мм. Пружина выбирает люфт и не
дает винту поворачиваться от вибрации. Заготовка подается слева. Барабан шириной
40 мм закрыт кожухом с патрубком для пылесоса. При установке на барабан
шлифшкурки №80 позволят снимать до 4 мм за проход.
|
Пример работы с насадкой.
|
Насадка №3
предназначена для обработки деталей произвольной формы. Под пластиковой крышкой
сформирована полость с присоединенным патрубком для пылесоса. Всасывание пыли
происходит через кольцевую щель вокруг барабана. Насадка очень помогает при
изготовлении шпангоутов , бимсов и т. п.
|
Пример
работы с приставкой. |
И в заключение еще кратко о приставке к ручному лобзику,
работа на котором тесно связана со станком, описанным выше.
|
Собственно доработка свелась к изготовлению нового столика к
ручному лобзику. Столик фиксируется также, как и штатный. Сам лобзик жестко
зажимается в столярном верстаке.
|
Столик
изготовлен из 10мм фанеры, область вокруг пилки и в месте крепления к лобзику
усилена алюминиевой 3мм пластиной, остальное пространство заполняет
пластик.
|
Увеличенный
фрагмент предыдущего фото. Показаны возможности реза узкой пилкой, у которой
закруглена задняя кромка. Ширина пропила около 1,5
мм.
|
Собственно весь процесс изготовления детали состоит в ее
выпиливании лобзиком с запасом 1-2 мм, а затем точной подгонке на шлифовальном
станке.
В заключение хочу отметить , что потраченное на изготовление
станка время (у меня ушло около 2-х месяцев работы по 2-3 часа в день) оправдало
себя полностью. Время изготовления деталей для модели значительно сократилось,
повысилось качество работы, после работы практически отсутствует пыль (кстати,
извлеченная из пылесоса пыль - прекрасная основа для шпаклевки). Система
автоматического регулирования скорости вращения двигателя работает надежно и
устойчиво, станок эффективно <грызет> дерево, при этом не допуская горение
и обугливание древесины.
©Игорь Капинос, 2005
|